Exemplo De Implantação Do Programa 5S Na Fabrica Da Toyota – Exemplo De Implantação Do Programa 5S Na Fábrica Da Toyota: este estudo de caso analisa a implementação bem-sucedida do programa 5S na renomada fábrica da Toyota, destacando as estratégias e os resultados alcançados. A metodologia 5S, composta por Seiri (Senso de Utilização), Seiton (Senso de Ordenação), Seisō (Senso de Limpeza), Seiketsu (Senso de Saúde/Higiene) e Shitsuke (Senso de Autodisciplina), é fundamental para a otimização de processos e a melhoria contínua, pilares da filosofia Toyota.
Exploraremos como cada etapa do 5S foi aplicada, os desafios enfrentados e o impacto positivo na produtividade, segurança e redução de custos.
Através de exemplos práticos e dados concretos, demonstraremos a eficácia do programa 5S na fábrica Toyota, fornecendo insights valiosos para empresas que buscam implementar metodologias de melhoria contínua em seus ambientes de trabalho. A análise abrange desde a organização do espaço físico até a padronização de processos e a promoção da autodisciplina entre os colaboradores, mostrando como a cultura organizacional da Toyota contribui para o sucesso da iniciativa.
Introdução ao Programa 5S na Toyota
O sucesso da Toyota, sinônimo de eficiência e qualidade, não se deve apenas à sua tecnologia de ponta, mas também a uma filosofia de gestão enxuta que permeia todos os seus processos. Um pilar fundamental dessa filosofia é o programa 5S, um método de organização e otimização do ambiente de trabalho que, apesar de sua aparente simplicidade, tem um impacto profundo na produtividade e na cultura da empresa.
Vamos desvendar como a Toyota implementou e se beneficia do 5S, com um toque de humor e muita informação relevante.
O 5S, acrônimo para Seiri (Senso de Utilização), Seiton (Senso de Ordenação), Seisō (Senso de Limpeza), Seiketsu (Senso de Saúde/Higiene) e Shitsuke (Senso de Autodisciplina), é muito mais que um simples programa de limpeza. Ele representa uma mudança de mentalidade, um compromisso contínuo com a melhoria, transformando o ambiente de trabalho em um espaço mais organizado, eficiente e seguro.
Para a Toyota, o 5S não é apenas uma ferramenta, mas um reflexo de sua cultura de respeito, precisão e melhoria contínua – a famosa filosofia Kaizen.
A aplicação do 5S na otimização dos processos fabris da Toyota resulta em redução de desperdícios, aumento da produtividade, melhoria da segurança e, consequentemente, aumento da lucratividade. Imagine uma fábrica onde tudo está no seu lugar, limpo e organizado: o fluxo de trabalho se torna mais fluido, os erros diminuem, e os funcionários trabalham em um ambiente mais agradável e seguro, contribuindo para uma maior satisfação e motivação.
Benefícios da Implementação do 5S em uma Fábrica
Os benefícios da implementação do 5S são inúmeros e palpáveis. Desde a redução de acidentes de trabalho, até a otimização do tempo de busca de materiais e ferramentas, o 5S impacta positivamente em diversas áreas. A melhoria na qualidade dos produtos também é um benefício direto, já que um ambiente organizado contribui para a redução de erros e defeitos.
- Redução de custos com desperdícios de materiais e tempo.
- Melhora na segurança do trabalho, diminuindo acidentes e riscos.
- Aumento da produtividade e eficiência dos processos.
- Melhora na qualidade dos produtos e serviços.
- Ambiente de trabalho mais agradável e organizado, elevando a moral dos funcionários.
Seiri (Senso de Utilização): Organização do Espaço de Trabalho: Exemplo De Implantação Do Programa 5S Na Fabrica Da Toyota
A primeira etapa do 5S, o Seiri, foca na eliminação do desnecessário. Na Toyota, isso é levado a sério! Imagine a quantidade de itens que uma fábrica de automóveis acumula ao longo do tempo. Para lidar com isso, a Toyota utiliza métodos rigorosos de descarte e organização, otimizando o espaço e evitando acúmulo de itens desnecessários.
A Toyota compara constantemente diferentes técnicas de organização, buscando sempre a melhor solução para cada setor da fábrica. Eles analisam o fluxo de trabalho, a frequência de uso de cada item e a facilidade de acesso, buscando otimizar o espaço e evitar desperdícios de tempo e recursos.
Exemplos de Aplicação do Seiri na Toyota
Área | Item Removido | Método de Remoção | Descrição da Melhoria |
---|---|---|---|
Linha de Montagem | Ferramentas Obsoletas | Doação para instituição de caridade após inventário | Liberação de espaço, redução de riscos e otimização do fluxo de trabalho. |
Estoque de Peças | Peças com defeito ou fora de uso | Descarte adequado seguindo normas ambientais | Redução de custos com armazenamento e prevenção de acidentes. |
Escritório Administrativo | Documentos antigos e desnecessários | Digitalização e descarte seguro dos originais | Ganho de espaço e facilidade na busca de informações. |
Área de Reparos | Materiais em excesso e sem uso recente | Realocação para outro setor ou descarte, após análise de necessidade | Otimização do espaço e redução de custos com estoque. |
Seiton (Senso de Ordenação): Organização e Arrumação
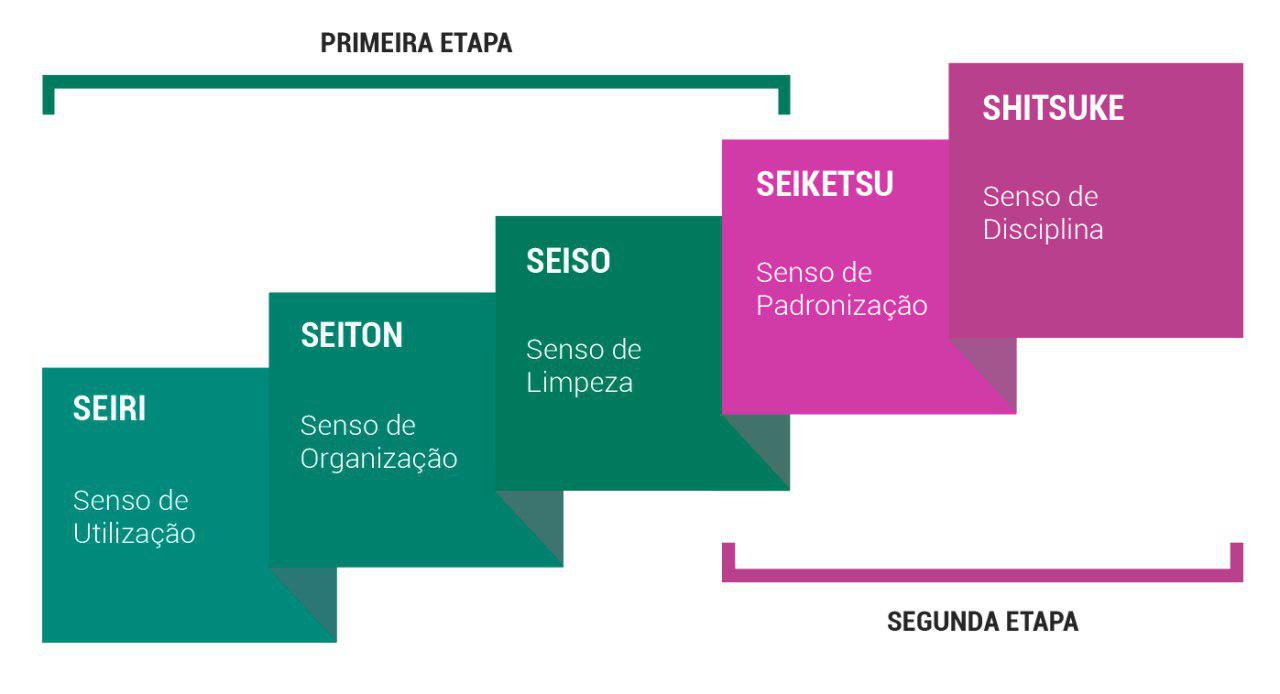
Após eliminar o desnecessário (Seiri), a Toyota aplica o Seiton, focando na organização e arrumação dos itens restantes. O objetivo é facilitar o acesso a ferramentas e materiais, reduzindo o tempo de busca e aumentando a eficiência. Imagine a diferença entre procurar uma chave de fenda em uma gaveta bagunçada e em uma gaveta organizada por tipo e tamanho!
A Toyota utiliza diversos métodos de etiquetagem e sinalização para garantir a clareza e a facilidade de localização de itens. Cores, etiquetas com informações detalhadas, e até mesmo sistemas de código de barras são empregados para garantir que cada item esteja no seu devido lugar.
Passos para Implementar um Sistema de Organização Eficiente
- Identificar todos os itens utilizados na área de trabalho.
- Classificar os itens por frequência de uso e importância.
- Definir locais específicos para cada item, de fácil acesso e visibilidade.
- Implementar um sistema de etiquetagem claro e eficiente.
- Criar um padrão visual que facilite a identificação e localização dos itens.
- Treinar os funcionários sobre o novo sistema de organização.
- Monitorar e ajustar o sistema conforme necessário.
Seisō (Senso de Limpeza): Manutenção da Limpeza
O Seisō, ou Senso de Limpeza, na Toyota vai além de uma simples limpeza superficial. É um processo contínuo de manutenção e prevenção, visando garantir um ambiente de trabalho limpo, seguro e livre de riscos. A limpeza não é vista como uma tarefa adicional, mas como parte integrante do processo produtivo.
A Toyota promove a responsabilidade pela limpeza entre os funcionários, incentivando a participação ativa de todos na manutenção do ambiente de trabalho. Cada funcionário é responsável pela limpeza de sua área de trabalho, contribuindo para um ambiente coletivamente limpo e organizado.
Processo de Limpeza e Manutenção em uma Linha de Produção Toyota
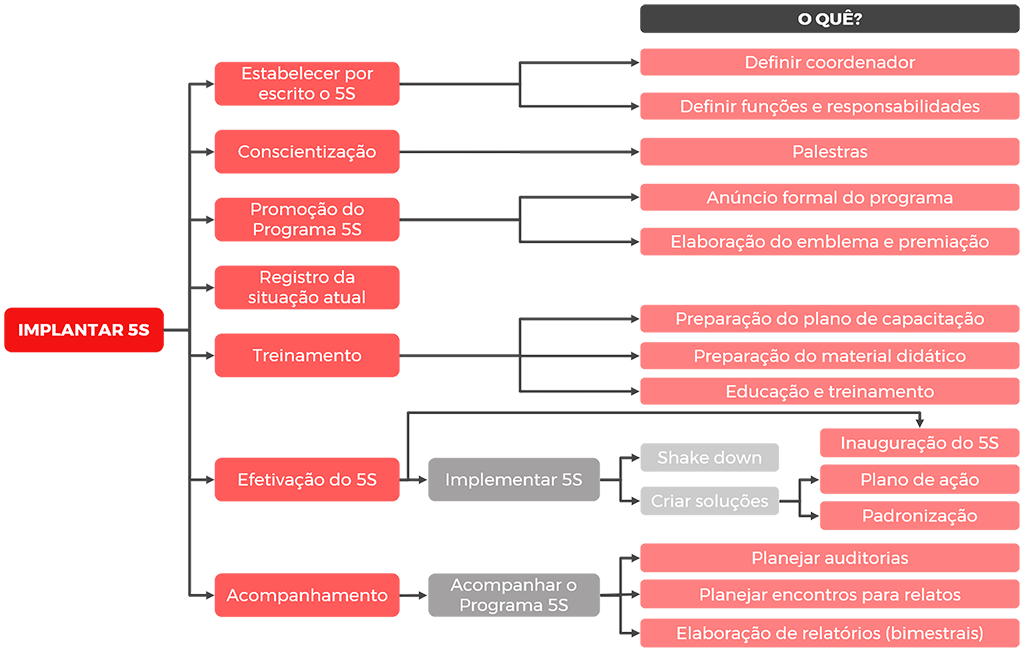
O processo de limpeza e manutenção é geralmente dividido em tarefas diárias, semanais e mensais. Tarefas diárias incluem a limpeza de máquinas e equipamentos após o uso, enquanto tarefas semanais podem envolver uma limpeza mais profunda de áreas específicas. Tarefas mensais podem incluir inspeções mais detalhadas e manutenção preventiva.
O processo segue um fluxo lógico: Inspeção visual -> Identificação de pontos críticos de sujeira/defeito -> Limpeza e organização -> Verificação final da limpeza e organização -> Registro e documentação. Este processo é repetido periodicamente, garantindo a manutenção da limpeza e organização.
Seiketsu (Senso de Saúde/Higiene): Padronização
O Seiketsu, ou Senso de Saúde/Higiene, concentra-se na padronização dos processos de organização e limpeza. A Toyota estabelece padrões claros e concisos, garantindo que a organização e a limpeza sejam mantidas consistentemente ao longo do tempo. Isso evita a deterioração do ambiente de trabalho e garante a eficiência do sistema 5S.
Indicadores-chave de desempenho (KPIs) são utilizados para monitorar a eficácia do 5S. Esses KPIs podem incluir métricas como o tempo de busca de materiais, a taxa de acidentes de trabalho, e o nível de organização do ambiente de trabalho. Acompanhamento constante garante que o sistema esteja funcionando conforme o esperado.
Manual de Procedimentos para Manter os Padrões do 5S
Um manual de procedimentos detalhado, incluindo check-lists, é essencial para manter os padrões do 5S. Este manual deve descrever os procedimentos para cada etapa do 5S, incluindo instruções detalhadas, imagens e exemplos práticos. Check-lists garantem que todos os passos sejam seguidos consistentemente.
Exemplo de check-list para a limpeza diária de uma estação de trabalho: [ ] Limpeza da superfície de trabalho; [ ] Limpeza das máquinas; [ ] Organização das ferramentas; [ ] Descarte de resíduos; [ ] Verificação de possíveis problemas.
Shitsuke (Senso de Autodisciplina): Manutenção dos Hábitos
O Shitsuke, ou Senso de Autodisciplina, é a etapa final e mais crucial do 5S. Ele representa a internalização dos princípios do 5S pelos funcionários, transformando-os em hábitos e práticas diárias. Na Toyota, a autodisciplina é promovida através de treinamento, incentivos e uma cultura organizacional que valoriza a organização e a limpeza.
Programas de treinamento e incentivo são utilizados para promover a adoção do 5S. A Toyota investe na capacitação dos seus funcionários, ensinando-os a importância do 5S e como aplicá-lo em seu dia a dia. Incentivos, como prêmios e reconhecimento público, também são utilizados para reforçar o comportamento desejado.
Cultura Organizacional da Toyota e a Autodisciplina
A cultura organizacional da Toyota, focada na melhoria contínua (Kaizen) e no trabalho em equipe, é fundamental para a manutenção do 5S. Ao contrário de algumas empresas que implementam o 5S como uma medida pontual, a Toyota integra o 5S à sua cultura, tornando-o um processo contínuo e integrado à rotina de trabalho. Esta abordagem integrada garante a sustentabilidade do programa a longo prazo.
Impacto da Implementação do 5S na Toyota
A implementação do 5S na Toyota teve um impacto significativo na produtividade, segurança e redução de custos. A organização e a limpeza do ambiente de trabalho contribuíram para um fluxo de trabalho mais eficiente, reduzindo o tempo de busca de materiais e ferramentas, e minimizando os erros.
A relação entre a implementação do 5S e a segurança do trabalho é direta e evidente. Um ambiente de trabalho organizado e limpo reduz o risco de acidentes, contribuindo para um ambiente mais seguro para os funcionários. Menos acidentes significa menos custos com afastamentos e tratamentos médicos.
Contribuição do 5S para a Redução de Custos e Desperdícios, Exemplo De Implantação Do Programa 5S Na Fabrica Da Toyota
O 5S contribui para a redução de custos e desperdícios de diversas maneiras. A eliminação de itens desnecessários reduz os custos de armazenamento, enquanto a otimização do fluxo de trabalho reduz o tempo de produção e os desperdícios de materiais. A prevenção de acidentes também reduz custos com reparos, tratamentos médicos e processos judiciais. Em resumo, o 5S é uma estratégia eficiente e eficaz para otimizar os recursos da Toyota e garantir a sua competitividade no mercado.